متالورژي پودر چيست؟
متالورژي پودر (Powder Metallurgy) نوعي فرآيند توليد است.
از اين روش براي توليد قطعات با دقت ابعادي بالا استفاده مي شود.
در يك فرآيند خاص، فلزات و آلياژهاي پودري آن ها در قالب هايي مشخص، در معرض فشار بالا قرار مي گيرند.
به اين ترتيب قطعه مورد نظر در خروجي از قالب به دست مي آيد.
بسياري از قطعاتي كه در زندگي روزمره با آن ها سروكار داريم، مبتني بر اين روش توليد مي شوند.
از جمله مي توان به بوش ها، ياتاقان ها و چرخ دنده ها اشاره كرد.
پايه و اساس اجراي موفقيت آميز متالورژي پودر، فرآيند تف جوشي (Sintering) است.
در اين فرآيند، مواد اوليه در معرض حرارت و فشار قرار مي گيرند تا ذرات پودري آن ها به يكديگر بچسبند.
در فرآيند تف جوشي، حرارت دهي به مواد اوليه فلزي تا نزديك نقطه ذوب آن ها صورت مي گيرد.
اين استراتژي باعث مي شود تا پيوندهاي ساختاري بين مواد فلزي كه به صورت پودري هستند، برقرار شود. در نهايت قطعه مورد نظر توليد مي شود.
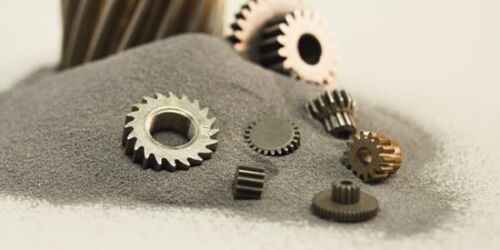
مراحل روش متالورژي پودر
اجراي فرآيند متالورژي پودر در چهار مرحله اساسي صورت مي گيرد كه در ادامه آن ها را شرح مي دهيم.
1 آماده سازي پودر
خواص هر محصولي تا حد زيادي وابسته به ويژگي هاي مواد اوليه اي است كه در توليد آن به كار مي روند.
فرآيند متالورژي پودر نيز از اين ماجرا مستثنا نيست؛
بنابراين در گام اول بايد نسبت به آماده سازي پودر اقدام كرد.
براي اين منظور معمولا از روشي تحت عنوان اتميزه كردن مواد مذاب استفاده مي شود.
در جريان اتميزه كردن مواد مذاب، فلز مايع به قطرات كوچكي تبديل مي شود و سپس سرد شده و هر يك از آن ها ذرات كوچكي را تشكيل مي دهند. به اين ترتيب پودر فلز توليد مي شود.
دستگاه اتميزه كردن فلزات معمولا از جريان آب با سرعت بالا براي پودر كردن ذرات فلزات استفاده مي كند.
اگرچه اتميزه كردن رايج ترين روش توليد پودر فلزات است؛ اما از روش هاي ديگري مانند رسوب الكتروليتي و تجزيه حرارتي نيز مي توان استفاده كرد.
با استفاده از تمام روش هاي فوق مي توان هر نوع ماده فلزي و آلياژهاي آن را به پودر تبديل كرد.
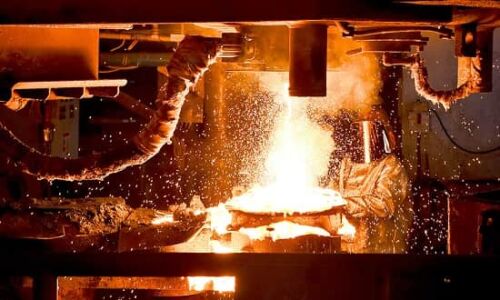
پودرهاي فلزات بايد از منظر فاكتورهاي زير براي استفاده در فرآيند متالورژي پودر ارزيابي شوند:
سرعت جريان
چگالي
تراكم پذيري
استحكام
2 مخلوط كردن پودرها
در مرحله دوم متالورژي پودر، بايد انواع پودرهاي مورد نياز براي توليد قطعه به همراه مخلوط كننده ها و روان كننده ها تركيب شوند.
تشخيص اين موضوع كه پودرها بايد با چه نسبتي با يكديگر تركيب شوند، نياز به دانش و تجربه بالايي دارد.
چرا كه تاثير به سزايي روي خصوصيات نهايي قطعات فلزي دارد.
بسته به نوع قطعه توليدي و مواد اوليه مي توان فرآيند اختلاط پودرها را در محيط هاي مرطوب يا خشك انجام داد.
چهار روش اصلي براي مخلوط كردن پودر فلزات وجود دارند كه عبارت اند از:
درام چرخان (rotating drum)
مخروط دوتايي دوار (rotating double cone)
ميكسر پيچي (screw mixer)
ميكسر تيغه اي (blade mixer)
3 فشرده سازي پودرها
در فرايند فشرده سازي، بايد پودرهاي تركيب شده در قالب خاصي تحت فشار قرار بگيرند تا شكل مورد نظر حاصل شود.
فشرده سازي بايد به گونه اي انجام شود تا فضاي خالي درون قطعه باقي نماند و چگالي آن ارتقا پيدا كند.
در صنايع مختلف بسته به نوع قطعه عمليات فشرده سازي تحت فشار بين 80 تا 1600 مگاپاسكال انجام مي شود.
دستگاه فشرده سازي پودرها عمليات فشرده كردن را در سه مرحله انجام مي دهد:
ابتدا پودرها وارد قالب شده و در معرض ارتعاش قرار مي گيرند تا منافذ درون قالب كاملا پر شوند.
در اين مرحله فشار به صورت محدود به پودر اعمال مي شود.
در پايان فشار نهايي در بالاترين سطح به پودر وارد مي شود؛
به گونه اي كه ذرات آن تغيير شكل داده و چگالي آن افزايش مي يابد.
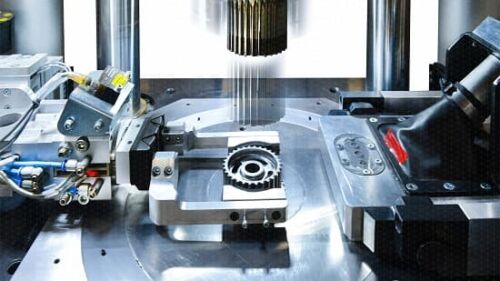
4 تف جوشي
در مرحله قبل عمليات فشرده سازي پودرها انجام مي شود؛ ولي شرايط به گونه اي رقم نمي خورد كه پيوند دائمي بين ذرات فلزي ايجاد شود.
براي برقراري پيوند دائمي بين ذرات فلزي در متالورژي پودر بايد آن ها در معرض حرارت قرار بگيرند تا با افزايش دما امكان برقراري پيوندها فراهم شود.
بنابراين در عمليات تف جوشي (Sintering)، قطعات حاصل از مرحله سوم تحت حرارت و فشار زيادي قرار مي گيرند.
همان طور كه اشاره كرديم، حرارت اعمال شده تا قبل از نقطه ذوب ذرات فلزي ادامه پيدا مي كند.
به اين ترتيب پيوند جديدي بين ذرات فلزي برقرار مي شود كه استحكام كافي براي توليد قطعه فلزي را دارند.
در جريان اين فرآيند كليه فضاي متخلخل موجود درون قطعات از بين مي روند و به اين ترتيب قطعات از نظر استحكام تقويت مي شوند.
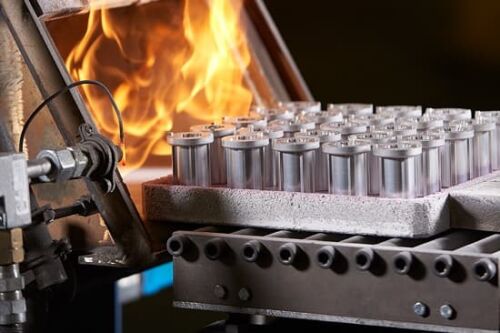
روش هاي متالورژي پودر
در حال حاضر 4 روش براي اجراي متالورژي پودر مورد استفاده قرار مي گيرند كه در ادامه به آن ها مي پردازيم.
1 متالورژي پودر به روش معمولي (Conventional)
در اين روش هر يك از مراحل چهارگانه اي كه در بالا برشمرديم به شيوه كلاسيك دنبال مي شوند.
روش عمومي كاملا شبيه به روشي است كه در گذشته هاي دور براي پياده سازي متالورژي پودر استفاده مي شد.
با اين تفاوت كه براي اجراي مراحل چهارگانه به جاي روش هاي سنتي از فناوري هاي مدرن استفاده مي شود.
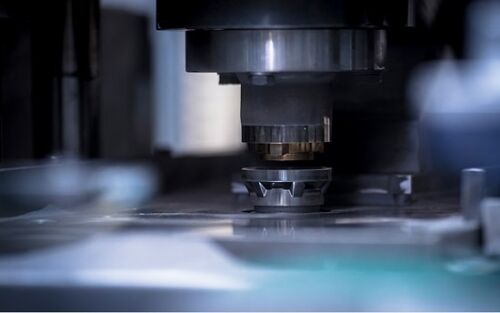
2 منالورژي پودر به روش قالب گيري تزريقي (Injection Molding)
از روش قالب گيري تزريقي مي توان در توليد قطعات با اشكال هندسي پيچيده در تيراژ بالا استفاده كرد.
معمولا در مرحله مخلوط كردن پودرها از نوعي چسب خاص شبيه به موم استفاده مي شود.
سپس پودرهاي تركيب شده وارد دستگاه قالب گيري تزريقي مي شود.
پس از عمليات فشرده سازي و تف جوشي درون دستگاه، چسب هايي كه در بالا اشاره كرديم به طور كامل متلاشي مي شوند.
به نوعي مي توان گفت كه قالب گيري تزريقي شباهت زيادي به روش قالب گيري پلاستيك در توليد محصولات پليمري دارد.
دفت ابعادي قطعات توليدي با اين روش مطلوب است؛ اما معمولا لازم است كه عمليات پرداخت كاري روي آن ها انجام شود.
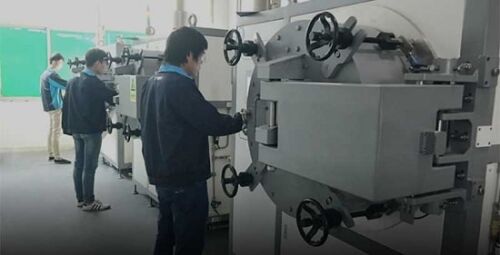
3 متالورژي پودر به روش پرس ايزواستاتيك (Isostatic Pressing)
در روش متالورژي پودر با پرس ايزواستاتيك، فشار يكسان به كل سطح قطعه كار اعمال مي شود.
به اين ترتيب قطعه از نظر ساختاري كاملا يكپارچه خواهد شد.
پرس ايزواستاتيك را مي توان بسته به نوع مواد اوليه و قطعه مد نظر به صورت سرد يا گرم انجام داد.
معمولا براي توليد قطعات با ابعاد بزرگ و پيچيده از پرس سرد استفاده مي شود.
فشاري كه به وسيله پرس روي قطعه كار اعمال مي شود بين 5000 تا 100000 پوند بر اينچ مربع متغير است.
پرس ايزواستاتيك گرم باعث مي شود كه تخلخل درون قطعات به طور كامل از بين رفته و محصول نهايي با چگالي بالايي به دست بيايد.
بنابراين خواص مكانيكي قطعاتي كه با پرس گرم توليد مي شوند تا حدودي بهتر از پرس سرد است.
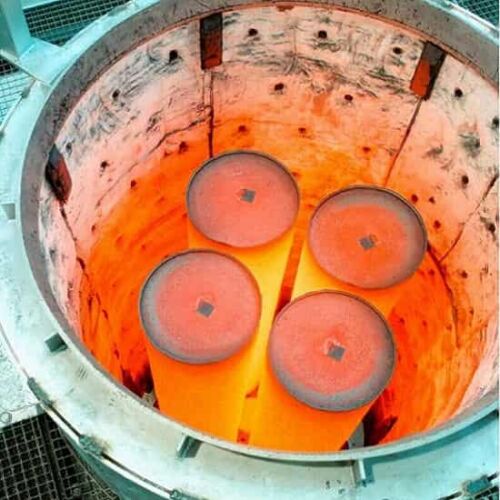
4 متالورژي پودر به روش افزودن فلز (Metal Additive)
از اين روش بعضا تحت عنوان چاپ سه بعدي قطعات فلزي نيز ياد مي شود كه به عنوان فناوري جديد متالورژي پودر به حساب مي آيد.
معمولا از روش افزودن پودر براي توليد سريع و كم هزينه قطعات نمونه استفاده مي شود.
با استفاده از اين روش معمولا ضايعاتي از مواد اوليه باقي نمي ماند.
همچنين فناوري ليزر براي اجراي مرحله تف جوشي استفاده مي شود.
به اين ترتيب دقت ابعادي بالايي نيز در توليد محصولات فلزي به دست مي آيد.
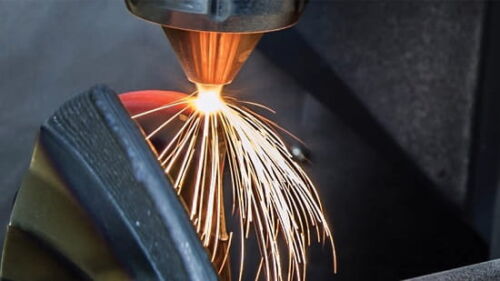
كاربرد متالورژي پودر
توليد به روش متالورژي پودر با توجه به پيشرفت هاي تكنولوژي ضايعات كمتري به دنبال دارد.
همچنين به كمك اين روش مي توان قطعات را در تيراژ بالا و با دقت ابعادي مناسب توليد كرد.
به همين دليل در بسياري از صنايع از اين روش براي توليد محصولات فلزي استفاده مي شود.
در همين راستا از جمله مهم ترين تجهيزاتي كه با استفاده از اين روش توليد مي شوند، مي توان به موارد زير اشاره كرد:
اجزاي فرمان خودرو
اجزاي سيستم انتقال قدرت خودرو
درپوش ياتاقان خودرو
اجزاي سيستم سوخت رساني خودرو
ديسك توربين موتور جت
پروتز زانو
تيغ هاي جراحي
انواع و اقسام چرخ دنده ها
ابزارهاي برش كاري فلزات
شيرآلات و منيفولدها
ابزارهاي فني مانند پيچ گوشتي و انبر
انواع فلزات قابل استفاده در متالورژي پودر
اشاره كرديم كه از بسياري از فلزات مي توان براي توليد محصولات مختلف به روش متالورژي پودر استفاده كرد.
البته برخي از فلزات هستند كه به دليل خواصشان معمولا بيشتر استفاده مي شوند.
مهم ترين عواملي كه در زمان انتخاب مواد اوليه بايد مد نظر قرار بگيرند، عبارت اند از:
مقاومت در برابر خوردگي
سختي
استحكام كششي
چقرمگي
استحكام خستگي
اگر فلزي در هر 5 فاكتور فوق از وضعيت مطلوبي برخوردار باشد، با خاطري آسوده مي توانيد از آن استفاده كنيد.
در همين راستا از جمله پركاربردترين مواد اوليه فلزي مي توان به موارد زير اشاره كرد:
1 فولاد ضد زنگ
مهم ترين خصوصيات فولاد ضد زنگ مقاومت بالا در برابر خوردگي و زنگ زدگي است.
بهترين نوع فولادهاي ضد زنگ قابل استفاده در فرآيند متالورژي پودر، سري 300 و 400 آن هاست.
از اين مواد اوليه براي توليد قطعات تجهيزات هوايي، قطعات خودرو، ابزارهاي پزشكي و… استفاده مي شود.
2 مس
معمولا از پودر مس براي توليد آلياژهايي استفاده مي شود كه خواص فيزيكي بسيار خوبي دارند.
برنز يكي از اين مواد آلياژي است كه از تركيب مس و قلع توليد مي شود.
از برنز براي توليد بلبرينگ استفاده مي شود.
3 نيكل
نيكل علاوه بر مقاومت بالا در برابر خوردگي، تحمل دماي بالايي نيز دارد.
به همين دليل براي ساخت قطعات توربين هاي گازي و موتور موشك با روش متالورژي پودر از نيكل استفاده مي شود.
تركيب نيكل با مس، آلياژي بسيار سخت را ايجاد مي كند كه در برابر آب شور نيز مقاوم است.
از تركيب آلياژ نيكل مي توان براي توليد قطعات فلزي كشتي استفاده كرد.
نيكل خاصيت انعطاف پذيري خوبي دارد كه امكان شكل پذيري آن را ارتقا مي دهد.
نيكل در متالورژي پودر
4 آلومينيوم
آلومينوم فلزي نرم، بسيار انعطاف پذير و همچنين سبك است.
معمولا از آلومينيوم در تركيب با فلزات ديگر براي توليد به روش متالورژي پودر استفاده مي شود.
آلومينيوم سازگاري بالايي دارد و با طيف گسترده اي از مواد تركيب مي شود.
در صنعت هوافضا و خودروسازي از آلومينيوم به وفور استفاده مي شود.
5 آهن
آهن به تنهايي فلزي نرم به حساب مي آيد و به همين دليل با كربن تركيب مي شود تا فولاد توليد شود.
در عين حال در بين انواع فلزات، تقريبا بيشترين ماده مورد استفاده براي توليد قطعات به روش متالورژي پودر، آهن است.
از پودر آهن براي توليد برخي قطعات خودرو مانند شفت استفاده مي شود.
6 تيتانيوم
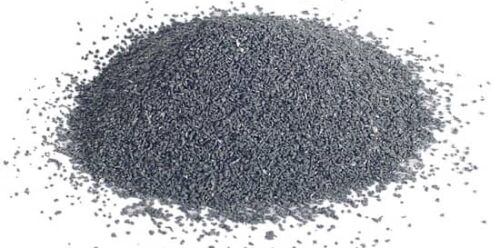
تيتانيوم گران ترين فلزي است كه براي توليد به روش متالورژي پودر استفاده مي شود.
تيتانيوم در ظاهر نقره اي رنگ است؛ ولي پودر آن به رنگ خاكستري يا سياه در مي آيد.
استحكام بسيار بالايي دارد و همين موضوع دليل اصلي قيمت بالاي تيتانيوم است.
در توليد قطعات هواپيما و موشك از پودر تيتانيوم استفاده مي شود.
مزاياي متالورژي پودر
اجراي روش متالورژي پودر نيازمند صرف زمان زيادي است.
به همين دليل ممكن است بسياري در وهله اول ساير روش هاي توليد را ترجيح دهند.
اما نبايد فراموش كنيد كه پيشرفت هاي تكنولوژي، هزينه توليد به اين روش را تا حد زيادي كاهش مي دهد.
در كنار آن از جمله مهم ترين مزاياي متالورژي پودر مي توان به موارد زير اشاره كرد:
1 سازگاري با محيط زيست
بيش از 97 درصد مواد اوليه اي كه براي توليد به روش متالورژي پودر استفاده مي شوند، تبديل به محصول نهايي مي گردند.
به همين دليل اين روش سازگاري بالايي با محيط زيست دارد.
سازگاري متالورژي پودر با محيط زيست
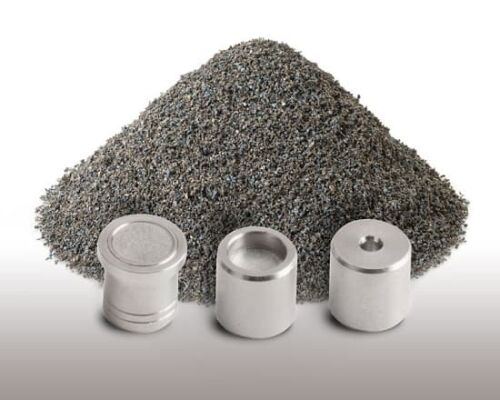
2 انعطاف پذيري
امكان تركيب مواد اوليه غير فلزي به همراه فلزات براي توليد محصولات مختلف با اين روش وجود دارد.
اين در حالي است كه در ساير روش هاي توليد به ندرت چنين امكاني وجود دارد.
به علاوه اين كه از اين روش مي توان براي توليد قطعات با شكل هاي هندسي پيچيده نيز استفاده كرد.
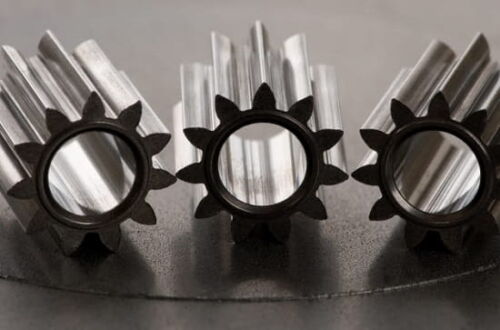
3 كاهش نياز به پردازش قطعه
ما را در سایت ارائه مطالب علمی، تخصصی و عمومی در مورد استیل دنبال می کنید
برچسب : نویسنده : امید احمدی بازدید : 102 تاريخ : چهارشنبه 21 دی 1401 ساعت: 13:06